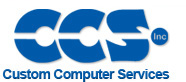 |
 |
View previous topic :: View next topic |
Author |
Message |
jecottrell
Joined: 16 Jan 2005 Posts: 559 Location: Tucson, AZ
|
Hardware Question: Battery Life Testing |
Posted: Thu Mar 03, 2005 1:59 pm |
|
|
I'm reaching the final stages of my first project and I had a question about battery life testing.
Background:
9V battery
MCP1701 3.3V LDO
18F2525
Firmware RTC
2 LEDs (used for debugging)
Serial I/O (not available during normal operation)
I would like to test the battery life and the first idea was to put the current time/date into EEPROM every minute and wait for the battery to die. I would then read the EEPROM to see when the last time was written. The only issue I can see is if, after it browns out and comes up for more than a minute a new and incorrect time will get written.
Having never done this before, I yield to the experts for ideas....
Thanks,
John |
|
 |
PCM programmer
Joined: 06 Sep 2003 Posts: 21708
|
|
 |
Mark
Joined: 07 Sep 2003 Posts: 2838 Location: Atlanta, GA
|
|
Posted: Thu Mar 03, 2005 2:11 pm |
|
|
Just monitor the voltage of the battery and log it. You should know the minimum input voltage of the circuit. You can get a rough idea by measuring the current draw and knowing the capacity of the battery. |
|
 |
Ttelmah Guest
|
|
Posted: Thu Mar 03, 2005 4:14 pm |
|
|
Seriously, get rid of the 9v battery!. You are wasting a huge amount of the power available. Assume the battery has a real 9v starting voltage, and droops to perhaps 7.5v, before falling away completely. When you start, your regulator, even if perfectly efficient, will be simply dissipating 63% of the power drawn from the battery. Even as the battery goes completely flat, it'll still represent half the losses. You want a battery source whose 'end point' voltage, is just above the minimum for your regulator. Probably about 4.5 to 5v. In the same size, a 4.5v battery, will have about twice the Ah rating available, doubling the useable time, since with a linear regulator the current will be constant. Alternatively, go with a switching 'boost' regulator, designed to operate off a 1.5v cell. These will usually be over 90% efficient, and a 1.5v cell the same size as the 9v battery will give about six times the Ah rating, while the inverter will draw just over twice the current. Again you more than double the duration the system will run for, for the same amount of stored power in the battery!...
Best Wishes |
|
 |
PCM programmer
Joined: 06 Sep 2003 Posts: 21708
|
|
Posted: Thu Mar 03, 2005 4:20 pm |
|
|
But sometimes the product's enclosure determines the battery type.
If the box that you want to use only comes with a 9v battery door,
then you have to use it. Our one product that uses a 9v battery
will last for at least 100 hours. It's an instrument that's only used
occasionally and it has auto-shutoff after one hour. |
|
 |
jecottrell
Joined: 16 Jan 2005 Posts: 559 Location: Tucson, AZ
|
Battery Life Testing |
Posted: Thu Mar 03, 2005 6:58 pm |
|
|
I've got to admit Ttelmah has a point. I'm working on a low power design (the Nanowatt part should be a clue....) I ended up with a 9V battery because I had some extra clips....(really bad excuse.) Luckily, I haven't committed to an enclosure or anything that would lock me into that choice.
Unfortunately, I'm committed (in the short term) to the MCP1701 LDO...my third revision board just arrived today. I will start looking into your recommendations. Not having and EE background my intuition prevented me from seeing the big picture.....maximize energy density and efficiency, or at least take both factors into account.
What switching boost regulator would you recommend? I need mainly, availability. I have found that there are all sorts of great parts, but the one that is perfect for the job is never available in small quantities for prototyping. I typically need a 3.3V @ 50mA or 5.0V @ 250mA (not on the same board/design). Other requirements are low peripheral part count and no smaller than an SOIC/SOT type package.
Thanks again, I'll go Googling and await an answer.
John |
|
 |
Ttelmah Guest
|
|
Posted: Fri Mar 04, 2005 3:53 am |
|
|
The 'boost' solution is the way to go to maximise available power. The 'downside' is that most have some significant 'standby' current if you put your circuit to sleep. The 'best' here, are from some odd suppliers (in the UK, Zetex), or companies like Maxim, who can be a pain to get parts from... National Semi, are good, in that most parts they list are genuinely available, but their best part, still draws perhaps 1uA, when shutdown (they claim 2uA, but I have never seen an example this bad).
For simplicity, and best overall power useage, on a system using a standby mode, I'd suggest the 3*AA solution, with the LDO. AA batteries, have just about the highest energy stored per unit volume of any cell (basically a lot of work has been put into these by the battery manufacturers). Fairly closely followed by AAA cells. This keeps things really simple, and is probably the best 'compromise'. These are also the cheapest batteries available in general. If you look at 'mass production' electronics, most use these batteries now, with 2 off, 3 off, and 4 off packs being very common. Most remote controls use 2*AA, without any regulation at all.
Best Wishes |
|
 |
MGP
Joined: 11 Sep 2003 Posts: 57
|
|
Posted: Fri Mar 04, 2005 6:32 pm |
|
|
Another solution to the problem (assuming you still want to use the 9V battery) is to use a very efficient step down (buck) switching regulator. TI has some great parts that are about 90%+ efficient and work at 600KHz-1MHz. They have on-board switches and synchronous rectification and because of their switching frequency use very small external components (small inductor and chip capacitors).
I just built a MPS430 based handheld device that uses a 8.4V (2 cell) lithium ion battery pack. I needed 3.3V and 5V for my hardware and used the TPS62xxx devices. Very efficient and each circuit can fit in about the space of a dime.
Maxim and Linear Technology also have similar devices. |
|
 |
valemike Guest
|
|
Posted: Fri Mar 04, 2005 8:25 pm |
|
|
For voltage regulators, PCMPro and Kenny suggested a few months ago a Seiko part and a MAX666. I ended up going with the MAX666 part --- 9V battery input voltage, voltage divider to get 3.3V, and it only uses something like 5ua. (I think the seiko part uses less uA). You can check that out.
I was going to just go with 2 AA's in series, but i needed the 9V battery to buzz a 12V beeper. 99.99% of the time, my PIC is asleep however |
|
 |
Guest
|
|
Posted: Sun Mar 06, 2005 2:11 pm |
|
|
I don�t understand why not using a 3,6v, high capacity battery.
You have Tadiran�s ER14505 wich are GREAT. |
|
 |
PCM programmer
Joined: 06 Sep 2003 Posts: 21708
|
|
Posted: Sun Mar 06, 2005 3:40 pm |
|
|
A lot of the battery selection process has to do with the enclosure.
Let's look at Pactec enclosures -- at some of their handheld cases.
The HR series uses either 9v or two AA's.
http://www.pactecenclosures.com/Plastic-Enclosures/HR-Series.html
Look at the HM series. Again, it's the same thing, 9v or AA.
http://www.pactecenclosures.com/Plastic-Enclosures/HM-Series.html
You have to go with a case that:
1. Is acceptable to the customer, in both shape and color.
2. Is available in quantity (now) at a reasonable price.
3. Is large enough to hold your board and other components.
On one project, we looked at using re-chargable NimH, and other types.
I didn't like the cost, and some of the battery types would explode
if you didn't charge them correctly. Do I as an engineer want to set
myself to be hit by lawyers 1 or 2 years downstream ? Hell, no.
So I design in a safer battery technology. All that alkaline does, is leak
if it goes bad. Maybe you have to replace a case, but it doesn't blow up.
Two alkaline AA batteries have basically the same energy as one of
those Tadiran TL-5104 batteries that you suggested. The two AA's
cost maybe $ .21 or .25 (US) each in 1K quantity. The TL-5104 costs
$3.57 at 1K. These are Digikey prices. So that's maybe $.50 vs. $3.50, let's say.
However, the alkaline batteries decline in voltage over time. They
start at 1.58v and are considered to be discharged at .80v.
So you need to use a boost regulator to keep a constant 3.3v out.
We used a T.I. TPS61107PWR for this. Digikey wants $2.40 (US) in 500
for them. Plus, you need an expensive low ESR tantalum cap on the
output, and the inductor, so the real the real cost is easily $3.50 for
the boost converter circuit. The TPS61107 also has a 1.8v LDO on it,
that we needed for another chip, so you could find a cheaper boost
converter solution if it was a pure 3.3v circuit.
So the lithium solution is somewhat cheaper initially, but once you run
through your first battery, the alkaline solution is much cheaper. You
get about 7 watt-hours of energy for $.50 (US). The lithium replacement
cost for the same energy is $3.50 and that's OEM pricing. If the customer
has to replace it, it's much more expensive.
This is getting kind of long, but one more thing is that the cases (Pactec
or others) are not built to handle a single AA. They're also not built
to handle two AA's in parallel, which is a possible solution with the
lithiums. But you really can't do that, because the battery orientation
is molded into the plastic case, and you sure don't want to confuse the
customer. And the customer might go buy two alkalines and try to
make them work, and they don't, which generates a costly tech support
call.
If this is a hobby project, you can do whatever you want, but if it's
commercial a lot more goes into the decision. |
|
 |
|
|
You cannot post new topics in this forum You cannot reply to topics in this forum You cannot edit your posts in this forum You cannot delete your posts in this forum You cannot vote in polls in this forum
|
Powered by phpBB © 2001, 2005 phpBB Group
|